
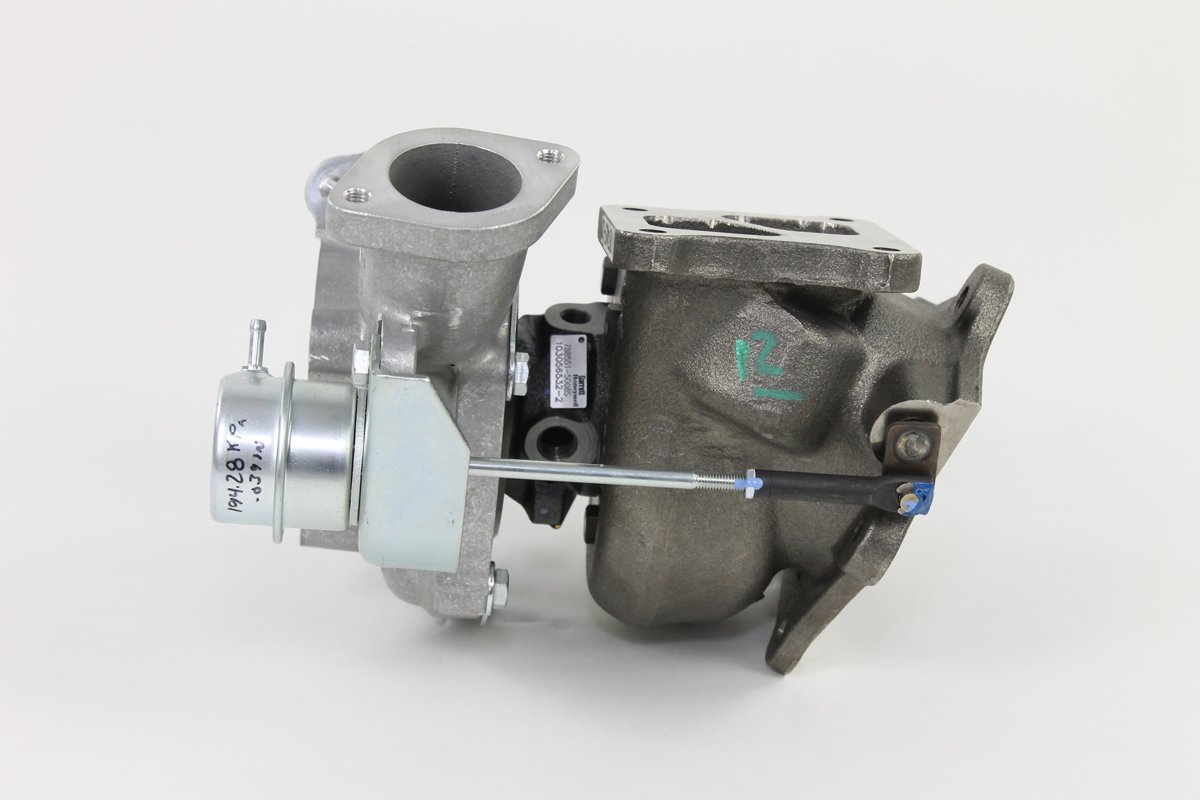
The operating principle is the same as older manual boost controllers, which is to control the air pressure presented to the wastegate actuator. Most modern designs are electronic boost controllers that use an electronic control unit to control the boost via a solenoid or stepper motor. Some systems use a solenoid in conjunction with a stepper motor, with the stepper motor allowing fine control and the solenoid coarse control. These designs allow fine control of airflow based on position and speed of the motor, but may have low total airflow capability. Īn alternative design is to use a stepper motor. Two-port solenoid bleed systems with a PID controller tend to be common on factory turbocharged cars. Solenoids may require small diameter restrictors be installed in the air control lines to limit airflow and even out the on/off nature of their operation. This effectively alters the flow rate of air pressure through the valve, changing the amount of air that is bled out instead of going to the wastegate's reference port. By varying the pulse width to the solenoid, the solenoid valve can be commanded to be open a certain percentage of the time.
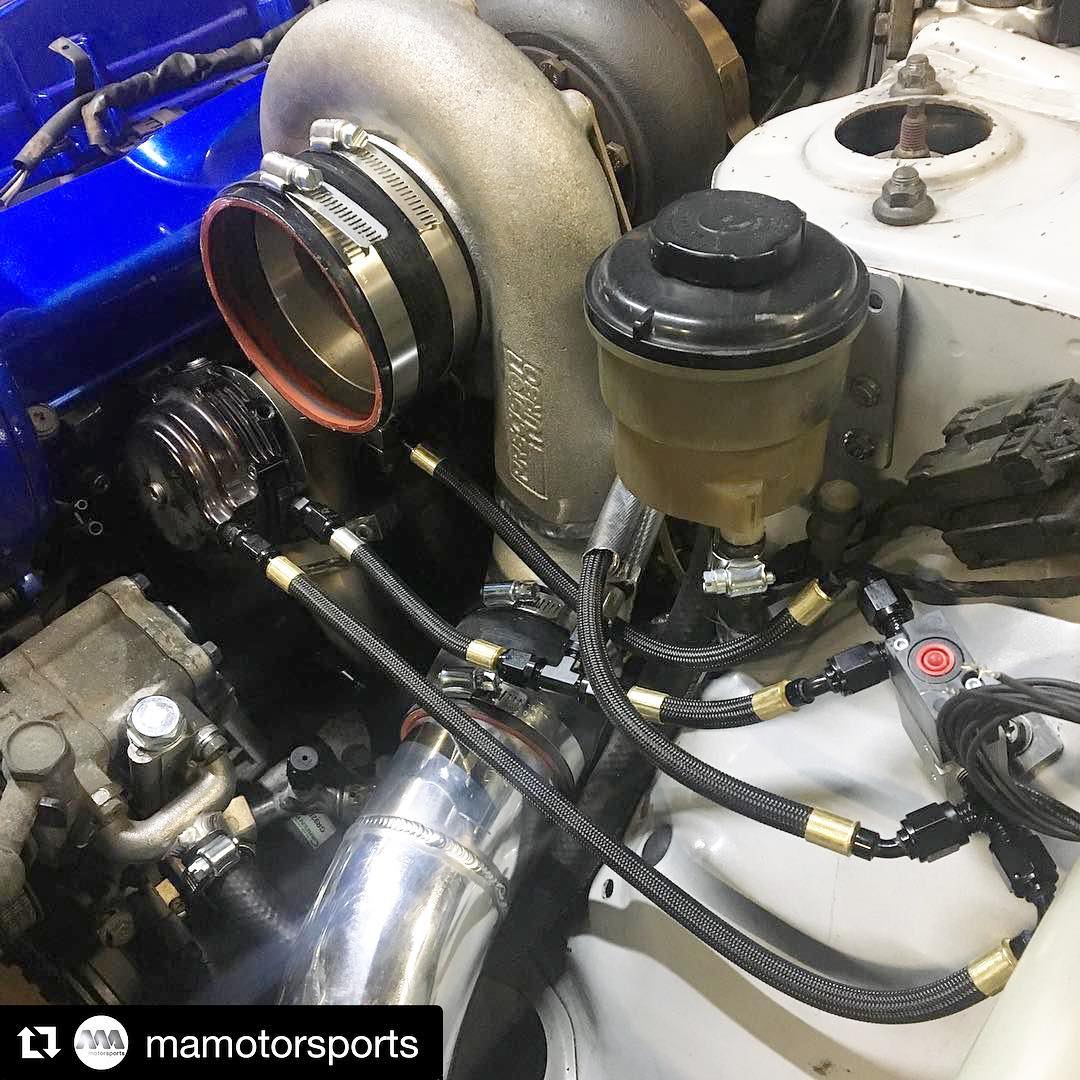
Many boost controllers use a needle valve that is opened and closed by an electric solenoid. The purpose of a boost controller is to reduce the boost pressure seen by the wastegate's reference port, in order to trick the wastegate into allowing higher boost pressures than it was designed for. A 4-port solenoid-type boost controller (used for a dual-port wastegate)
